Underground Fully Welded Ball Valves: Installation and Maintenance
In the intricate network of underground pipelines that crisscross beneath our feet, the role of specialized valves is paramount. Among these, Underground Fully Welded Ball Valves stand out for their technical prowess, providing a robust solution for the control and regulation of fluid flow in subterranean environments. This article delves into the technical features, installation procedures, and maintenance requirements of these ball valves.
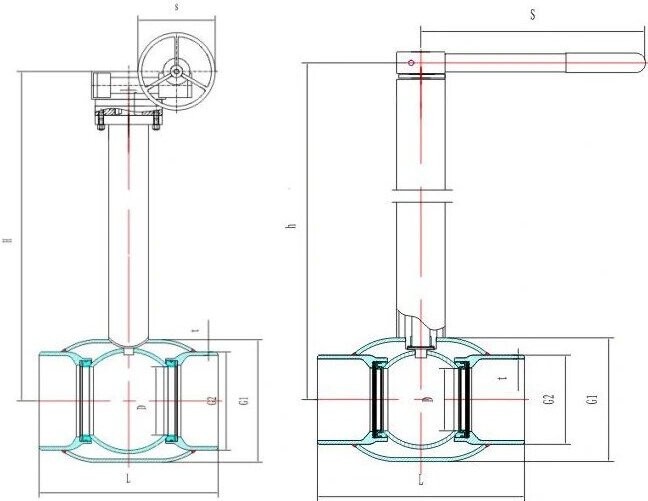
About Underground fully Welded Ball Valves
Underground fully welded ball valves play a crucial role in gas transmission pipelines due to their excellent technical features. These valves are manufactured using a fully welded construction method, creating a tightly integrated pipeline system that enhances the overall stress resistance and ability to withstand geological hazards, such as subsidence. Additionally, the fully welded design reduces the likelihood of gas leaks, while improving valve reliability, extending lifespan, and facilitating convenient installation and maintenance.
Pre-Installation Pressure Testing
Before installation, underground fully welded ball valves undergo pressure testing to ensure their integrity and safety.
Installation of Fully Welded Ball Valves
1. Hoisting
2. Welding
3. Valve Pit Construction
Daily Operations and Maintenance
To extend the valve lifespan, the following procedures should be followed for operation and maintenance.
2. Maintenance
The excellent technical characteristics of underground fully welded ball valves integrate the gas transmission pipeline seamlessly, enhancing overall stress resistance, geological hazard resilience, and minimizing the risk of gas leakage. These valves also exhibit improved reliability, extended lifespan, and offer convenient installation and maintenance.
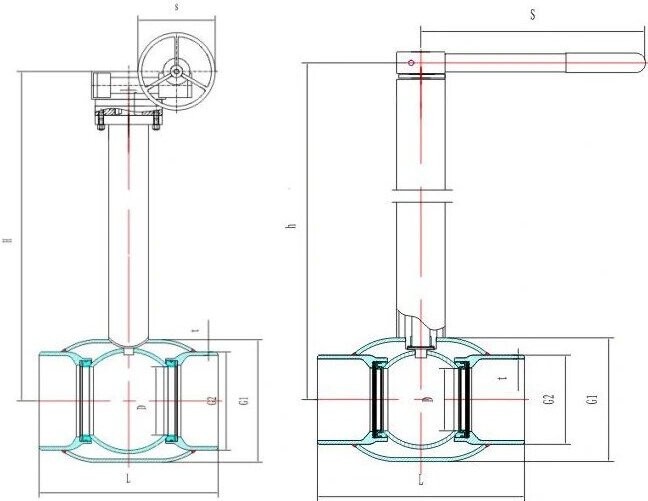
About Underground fully Welded Ball Valves
Underground fully welded ball valves play a crucial role in gas transmission pipelines due to their excellent technical features. These valves are manufactured using a fully welded construction method, creating a tightly integrated pipeline system that enhances the overall stress resistance and ability to withstand geological hazards, such as subsidence. Additionally, the fully welded design reduces the likelihood of gas leaks, while improving valve reliability, extending lifespan, and facilitating convenient installation and maintenance.
Pre-Installation Pressure Testing
Before installation, underground fully welded ball valves undergo pressure testing to ensure their integrity and safety.
1. Strength Test
Medium: Water
Valve opened to a 45-degree position, and water injected into the valve through the pressure testing valve on the sleeve pipe.
Pressure raised to 1.5 times the nominal pressure of the ball valve, maintained for 15 minutes with no leakage considered acceptable.
2. Tightness Test
Medium: Nitrogen
Valve closed, nitrogen injected into the valve to 1.1 times the nominal pressure.
Inspection for the absence of bubbles inside the valve within 5 minutes is considered satisfactory.
Medium: Water
Valve opened to a 45-degree position, and water injected into the valve through the pressure testing valve on the sleeve pipe.
Pressure raised to 1.5 times the nominal pressure of the ball valve, maintained for 15 minutes with no leakage considered acceptable.
2. Tightness Test
Medium: Nitrogen
Valve closed, nitrogen injected into the valve to 1.1 times the nominal pressure.
Inspection for the absence of bubbles inside the valve within 5 minutes is considered satisfactory.
Installation of Fully Welded Ball Valves
1. Hoisting
- Valves should be hoisted using the correct method, avoiding attaching lifting chains to handwheels, gearboxes, or actuators.
- Protective caps on both ends of the valve sleeve pipe should not be removed before welding.
2. Welding
- Welding is employed for the connection between the fully buried fully welded ball valve and the main pipeline.
- Weld seam quality must comply with the standards of Radiographic Testing of Fusion Welded Joints.
- When ordering valves, manufacturers should be requested to add 1.0m long sleeve pipes at both ends to allow for cutting and rewelding if the weld seam is found to be non-compliant.
3. Valve Pit Construction
- Special structural design is utilized, featuring maintenance-free characteristics.
- Prior to burial, a special anti-corrosion coating is applied to the outer side of the valve.
- Necessary extensions are made to the injection pipes for emergency grease filling of the valve seat and stem, the venting pipe, and the stem, allowing operators to perform various operations from the surface.
- After burial, constructing a small valve pit is sufficient, unlike conventional non-fully welded ball valves that require a large valve pit, resulting in a potentially hazardous confined space.
Daily Operations and Maintenance
To extend the valve lifespan, the following procedures should be followed for operation and maintenance.
1. Operation
- Regular operation prevents impurities from accumulating on the valve seat or ball surface, avoiding excessive local wear on the valve seat.
- Control the opening and closing time within an appropriate range to prevent excessive distortion load or prolonged wear on the valve seat surface due to medium flushing.
- When the valve is in operation, the ball should be fully open or fully closed to prevent damage to the valve seat.
2. Maintenance
- The valve seat chamber is the most prone to contamination; therefore, it should be cleaned annually.
- Regularly check the sealing performance of the valve through the drain nozzle.
- Valves on auxiliary gas lines are seldom adjusted; hence, they should be operated and injected with an appropriate amount of grease at least once a year to prevent bonding between the ball and the valve seat and sub-wear between the ball and the valve seat.
The excellent technical characteristics of underground fully welded ball valves integrate the gas transmission pipeline seamlessly, enhancing overall stress resistance, geological hazard resilience, and minimizing the risk of gas leakage. These valves also exhibit improved reliability, extended lifespan, and offer convenient installation and maintenance.