Maintenance and Cleaning Guide for Y-Type Strainer Screens
On this page
Y-type strainers are commonly used industrial filtration devices widely applied in various fluid transport systems. Their core component, the Y strainer screen, plays a crucial role in ensuring fluid purity and the proper functioning of equipment. This article will delve into the structure, function, maintenance considerations, cleaning methods, and the importance of strainer screens in specific industries to ensure their long-lasting effectiveness under high hygiene standards.
Understanding the basic concept of Y-type strainers is essential, but it is equally important to examine the structure and function of their core component, the strainer screen. The strainer screen directly impacts filtration effectiveness and overall system performance.
The strainer screen of a Y-type strainer primarily consists of a stainless steel mesh and a strainer frame, which together form an efficient filtration system.
Stainless Steel Mesh: Made from high-quality stainless steel, the mesh is resistant to corrosion, high temperatures, and pressure. The mesh aperture is designed according to specific application requirements to effectively retain targeted impurities. Common mesh sizes include 20 mesh, 30 mesh, and 50 mesh, with different sizes suitable for various filtration needs.
Strainer Frame: The mesh is securely installed within the frame, ensuring it maintains its shape under fluid pressure. The design of the frame also enhances the load-bearing capacity of the mesh and maintains stable filtration performance under high flow conditions.
Impurity Filtration: Through the stainless steel mesh, the Y-type strainer effectively removes solid particles, sediments, and other impurities from the fluid. This prevents wear and damage to downstream equipment, ensuring the normal operation of devices.
Fluid Protection: The strainer protects downstream equipment such as pumps, valves, and instruments, reducing equipment failure rates and maintenance costs. By improving the quality of the filtered fluid, production efficiency is enhanced, and the lifespan of the equipment is extended.
Flow Control: Some designs of Y-type strainers also feature flow regulation capabilities, allowing adjustments to the fluid flow rate according to demand, ensuring optimal fluid transport conditions.
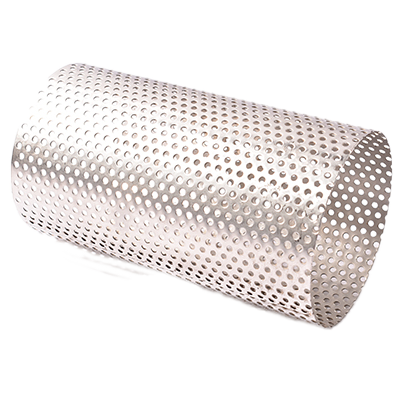
To maintain the efficient operation of the Y-type strainer screen, regular maintenance is essential. Here are some key maintenance points.
Over time, impurities will gradually accumulate within the strainer screen, leading to increased pressure and decreased flow rates. It is recommended that users conduct a thorough inspection at least once a month to ensure the strainer screen is in good condition. The inspection should include:
Accumulation of Impurities: Check the amount of impurities on the screen to assess whether it requires cleaning or replacement.
Integrity of the Stainless Steel Mesh: Inspect the mesh for deformation, cracks, or wear.
As a vulnerable component, particular care must be taken to protect the stainless steel mesh. During cleaning, avoid applying excessive force to prevent deformation or damage, which could compromise the filtration effectiveness during subsequent operations.
If deformation or damage is found during inspection, the screen should be replaced immediately. The replacement steps are as follows:
Shut Off Valves: Before replacement, close the valves on either side of the Y-type strainer that require inspection and replacement of the screen.
Disassemble the Strainer: Use a hook spanner to open the Y-type strainer, remove the screen support, and place the disassembled parts in a stainless steel sterilization box (which must be cleaned and sterilized before and after use).
Install New Screen: Remove the damaged screen and install a new one, then reassemble the strainer. Check the integrity and cleanliness of the new screen to ensure it meets design specifications, and document the process.
Regular cleaning of the strainer screen is a key step in maintaining the performance of the Y-type strainer. The following are specific steps for cleaning the screen.
Remove the Strainer Cover: Use a screwdriver to unscrew the bolts on the strainer cover for access to the screen.
Clear Impurities: Once opened, observe the screen, which may accumulate many impurities beneath it. Use appropriate tools (such as brushes or vacuum cleaners) to remove these impurities to prevent affecting subsequent filtration performance.
Rinse the Screen: Properly detach the screen and thoroughly rinse it with clean water to ensure cleanliness, removing any dirt adhered to its surface. Depending on the degree of contamination, a neutral detergent may be necessary.
Reinstall the Screen: After rinsing, reinstall the screen in the reverse order of disassembly and securely fasten the strainer cover screws.
The strainer screen of a Y-type strainer is a key component in ensuring fluid filtration efficiency and equipment protection. Through regular inspections, maintenance, and cleaning, users can effectively extend the service life of the screen, ensuring stable operation under high hygiene standards. Prioritizing the protection and management of the strainer screen not only enhances overall equipment performance but also reduces failure rates and increases production efficiency. By gaining a deep understanding of and effectively managing the Y-type strainer screen, companies can achieve higher safety and reliability in their fluid processing operations.