Structural Features and Advantages of the Orbit Plug Valve
On this page
The orbit plug valve is an industrial valve that combines sealing performance, durability, and operational flexibility. It is widely used in fields such as aviation fuel, natural gas, liquefied petroleum gas, and refined oil. Its unique structural design and multi-layered sealing system enable it to operate effectively under harsh conditions, ensuring system safety and stability. Below is a detailed explanation of the key structural features and performance advantages of the orbit plug valve.
When handling highly permeable, flammable, and explosive media such as aviation fuel, preventing leaks is crucial. The orbit plug valve employs a dual-sealing structure with an O-ring and spiral wound gasket at the center flange, effectively preventing leakage. This design is particularly suitable for high-risk applications like aerospace and petrochemicals. The double seal not only enhances pressure resistance and corrosion resistance but also improves the system's operational safety by minimizing potential hazards from leaks.
The valve's opening and closing involve both axial and rotational movements, which complicate the sealing process. The orbit plug valve uses a combination of inner and outer O-rings along with packing to create a multi-layered seal, ensuring reliable performance even under complex conditions. This design is especially effective when dealing with special media such as natural gas and liquefied petroleum gas, significantly enhancing the valve's sealing safety and long-term reliability, while reducing the risk of leaks due to packing wear or aging.
According to API 6D standards, all double-sealed valves must have pressure relief functions in the valve cavity. The orbit plug valve features three pressure relief systems, ensuring that cavity pressure is safely released under various operating conditions to prevent accidents caused by overpressure:
Manual Pressure Relief System: For manually operated valves, a needle valve is opened after the valve is closed to release cavity pressure into the upstream pipeline or atmosphere, addressing overpressure and checking the valve's sealing effectiveness.
Pressure Differential Relief System: Suitable for manual and electric-operated valves, this system automatically releases overpressure in the cavity to the upstream pipeline via a check valve and three-way structure, with a manual release valve for testing the seal.
Automatic Pressure Relief System: Designed for electrically operated valves, the pressure relief valve automatically opens when the valve is closed, connecting with the external environment or upstream pipeline to ensure pressure relief without manual intervention, guaranteeing system safety.
This multi-layered pressure relief design ensures the valve can effectively handle pressure fluctuations caused by environmental changes, preventing equipment failures or system ruptures due to rising pressure.
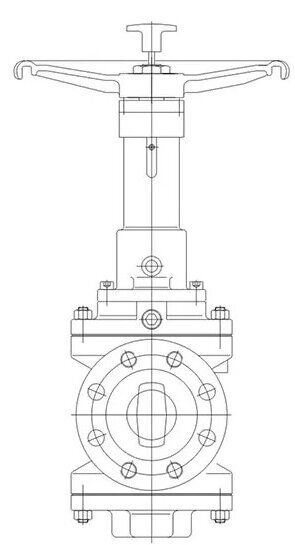
The orbit plug valve's operation mechanism adopts an L-shaped groove structure that separates the plug's axial linear movement from its 90-degree rotational movement. This design makes valve operation more effortless and flexible, reducing operational difficulty. The use of trapezoidal threads between the valve stem and the nut, featuring double or multiple heads, reduces the number of handwheel turns, improving operational efficiency.
Additionally, the valve is equipped with a gear transmission mechanism with a self-locking feature. The heavy-duty trapezoidal thread design handles larger loads, ensuring safe and reliable operation under various conditions.
To enhance the durability and reliability of the orbit plug valve under harsh conditions, critical components undergo special surface treatments.
The valve body's internal cavity is hard chrome-plated after grinding, providing excellent corrosion resistance, wear resistance, and erosion resistance.
The slider is hard chrome-plated to enhance the wear and corrosion resistance of the metal sealing surface.
The plug and upper and lower shafts are nickel-plated to improve rust and corrosion resistance.
The valve stem undergoes tempering followed by nitriding, achieving a surface hardness of over 900HV, significantly enhancing wear resistance and anti-galling performance.
These surface treatments not only improve the valve's durability but also enhance its ability to operate in high-pressure, high-temperature, and corrosive environments, ensuring long-term reliability.
The design of the orbit plug valve also considers the need for packing adjustments and maintenance during operation. Special windows are provided on both sides of the valve bracket, allowing on-line packing adjustment or replacement during operation. This reduces downtime and increases the convenience of maintenance, which is particularly valuable in high-risk, high-value industrial systems, minimizing the economic loss caused by system shutdowns.
The plug of the orbit plug valve adopts an integral cast structure, ensuring that the upper and lower shafts have sufficient stiffness and strength. High-precision bearings are used at the mating points between the upper and lower shafts and the valve cover, ensuring accurate positioning during operation and reducing friction and wear between the shaft and the bearing, thereby lowering operating torque and extending valve life.
To reduce the torque required during operation, especially for large-diameter valves, bearings are installed on both the upper and lower shafts to minimize friction between the plug and the bottom cover. For large-diameter valves where high friction might occur, the bottom cover is equipped with a tungsten carbide-coated bearing ring, and high-hardness balls are installed at the bottom of the sliders. These precision machining and material optimization techniques effectively reduce friction resistance, ensuring smooth operation and long-term stability.
By utilizing high-hardness materials and advanced surface treatment technologies, the orbit plug valve offers excellent corrosion and wear resistance over long-term use. This design allows the valve to perform reliably in harsh industrial environments, such as petrochemicals, natural gas transmission, and high-pressure pipeline systems, providing stable, low-maintenance operation over time.
The orbit plug valve achieves safe, reliable, and efficient operation in demanding conditions through its unique structural design, comprehensive sealing solutions, and multi-pressure relief systems. The use of high-quality materials and advanced processing not only extends the valve's service life but also ensures stable performance in various complex environments. Whether in aerospace, petrochemical, or natural gas transmission systems, the orbit plug valve is a key component for ensuring system safety and efficient operation.