Guide to Selection, Installment and Maintenance of Forged Steel Ball Valves
Forged steel ball valves are constructed with steel through the forging process, serving as a critical valve in controlling the flow of fluids in various industrial applications. These valves boast robust construction, durability, and versatility, making them a popular choice in piping system. This guide aims to provide comprehensive insights into the selection, installation, and maintenance of forged steel ball valves, ensuring optimal performance and longevity.
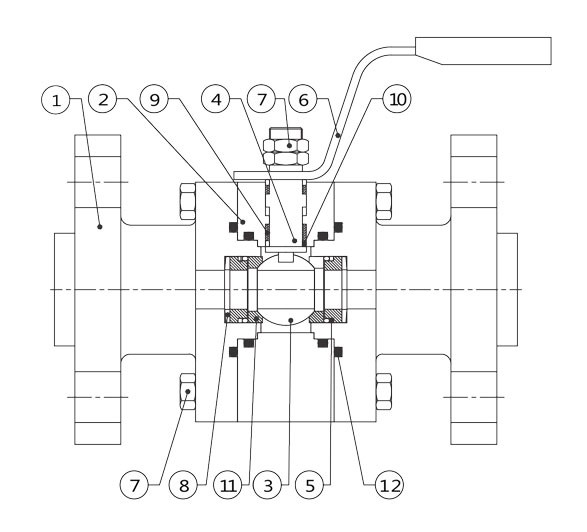
1. Selection Process: Meeting System Requirements
2. Installation and Sealing: Ensuring Integrity
3. Operation and Maintenance: Sustaining Longevity
4. Environmental and Safety Considerations
In conclusion, the selection and installation of forged steel ball valves demand a comprehensive approach. Considering working conditions, materials, correct installation procedures, and ongoing maintenance, coupled with strict adherence to safety measures, ensures the longevity, reliability, and safety of forged ball valves within diverse applications.
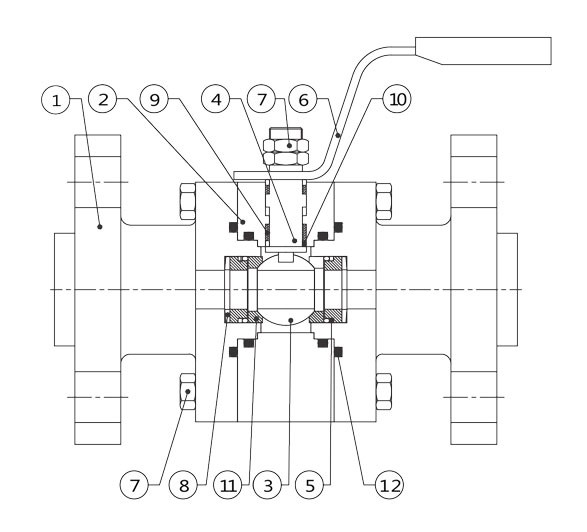
1. Selection Process: Meeting System Requirements
Understanding Working Conditions: The foundation of the selection process involves a detailed evaluation of specific working conditions and system requirements. Key parameters such as operating pressure, temperature, and medium characteristics must be thoroughly assessed to align with the demands of the application.
Material Considerations: Choosing the right materials is paramount. The acidity, alkalinity, and corrosiveness of the medium dictate the selection of materials, including options like carbon steel or alloy steel. A meticulous approach to material selection ensures compatibility and longevity.
Valve Specifications and Connection Methods: Tailoring valve specifications and connection methods to the unique needs of the application is crucial. A thorough understanding of the system's intricacies guides the selection of the appropriate valve specifications and connection methods.
Material Considerations: Choosing the right materials is paramount. The acidity, alkalinity, and corrosiveness of the medium dictate the selection of materials, including options like carbon steel or alloy steel. A meticulous approach to material selection ensures compatibility and longevity.
Valve Specifications and Connection Methods: Tailoring valve specifications and connection methods to the unique needs of the application is crucial. A thorough understanding of the system's intricacies guides the selection of the appropriate valve specifications and connection methods.
2. Installation and Sealing: Ensuring Integrity
Pre-Installation Inspection: Before installation, a comprehensive inspection of the valve's exterior and internal structure is imperative. Identifying damage or foreign objects ensures the valve's integrity and longevity.
Correct Orientation and Positioning: During installation, careful attention must be given to the proper orientation and positioning of the valve. Secure fastening and the use of suitable sealing materials are essential to prevent leaks and ensure optimal performance.
Correct Orientation and Positioning: During installation, careful attention must be given to the proper orientation and positioning of the valve. Secure fastening and the use of suitable sealing materials are essential to prevent leaks and ensure optimal performance.
3. Operation and Maintenance: Sustaining Longevity
Correct Switch Position and Handling: Ongoing attention to valve operation is crucial. Selecting the correct switch position and avoiding excessive force or rough handling prevents damage. Regular inspections of the operational status enable prompt repairs or replacements.
Exterior Cleanliness and Lubrication: Maintaining the exterior cleanliness of the valve and regular lubrication of moving parts contribute to its smooth and reliable operation over time. A proactive approach to maintenance ensures sustained performance.
Exterior Cleanliness and Lubrication: Maintaining the exterior cleanliness of the valve and regular lubrication of moving parts contribute to its smooth and reliable operation over time. A proactive approach to maintenance ensures sustained performance.
4. Environmental and Safety Considerations
Installation Environment: Environmental factors play a pivotal role in valve longevity. Installing valves in well-ventilated locations mitigates the impact of overheating, high temperatures, or severe vibrations.
Safety Measures: Operators must use appropriate protective gear and adhere strictly to operating procedures. Awareness of the valve's working pressure range is essential to prevent exceeding its load-bearing capacity.
Safety Measures: Operators must use appropriate protective gear and adhere strictly to operating procedures. Awareness of the valve's working pressure range is essential to prevent exceeding its load-bearing capacity.
In conclusion, the selection and installation of forged steel ball valves demand a comprehensive approach. Considering working conditions, materials, correct installation procedures, and ongoing maintenance, coupled with strict adherence to safety measures, ensures the longevity, reliability, and safety of forged ball valves within diverse applications.