Guide to Common Butterfly Valve Failures and Solutions
Butterfly valves, being widely used fluid control devices, may encounter various issues due to their complex structure and prolonged operation. In this comprehensive guide, we will delve into the potential failures of butterfly valves and provide detailed solutions to ensure the reliability and efficiency of these critical fluid control mechanisms.
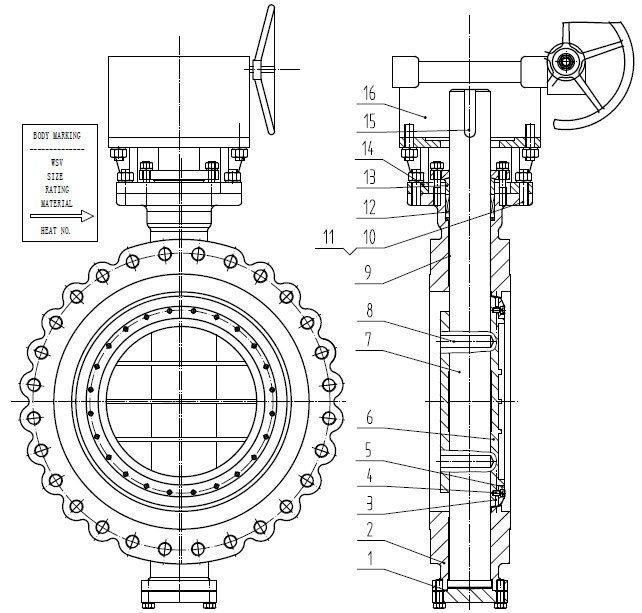
1. The Seal Leakage
2. Leakage at Both Ends of the Valve
4. Damage to Handles and Handwheels
6. Electric Installation Failures
By thoroughly understanding the potential causes of various butterfly valve failures and implementing these detailed solutions, we can effectively manage and maintain these crucial fluid control devices, ensuring prolonged and efficient operation.
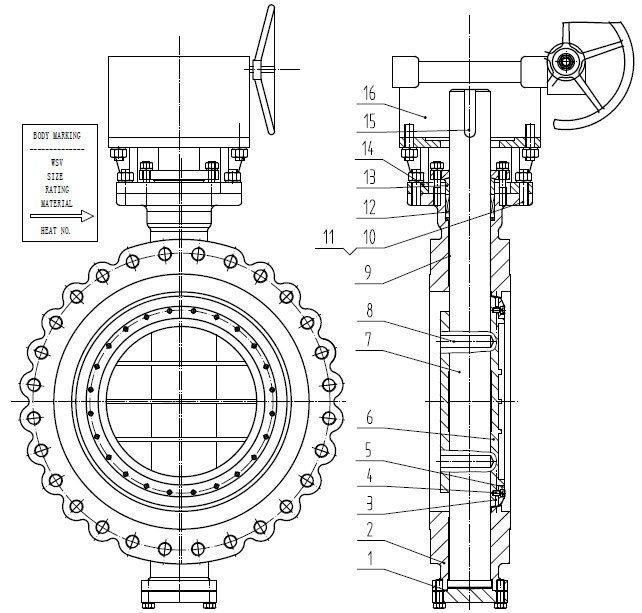
1. The Seal Leakage
Presence of Debris on Butterfly Plate and Sealing Ring:
One common cause of seal leakage is the presence of debris on the butterfly plate and sealing ring. To address this, it is essential to remove impurities and thoroughly clean the valve's internal cavity.
Misalignment of Butterfly Plate and Sealing Ring in the Closed Position:
Adjust the adjustment screws on the turbine or electric actuator to ensure proper alignment of the butterfly plate and sealing ring in the closed position, preventing leakage.
Uneven or Loose Flange Bolts at the Outlet:
Check the flange plane and bolt tightening force to ensure even and secure tightening, preventing potential leaks at the outlet.
Incorrect Pressurization Direction:
Follow the arrow indicating the sealing direction during pressurization to enhance the effectiveness of the seal.
One common cause of seal leakage is the presence of debris on the butterfly plate and sealing ring. To address this, it is essential to remove impurities and thoroughly clean the valve's internal cavity.
Misalignment of Butterfly Plate and Sealing Ring in the Closed Position:
Adjust the adjustment screws on the turbine or electric actuator to ensure proper alignment of the butterfly plate and sealing ring in the closed position, preventing leakage.
Uneven or Loose Flange Bolts at the Outlet:
Check the flange plane and bolt tightening force to ensure even and secure tightening, preventing potential leaks at the outlet.
Incorrect Pressurization Direction:
Follow the arrow indicating the sealing direction during pressurization to enhance the effectiveness of the seal.
2. Leakage at Both Ends of the Valve
Failure of Sealing Gaskets on Both Sides:
Replace the faulty sealing gaskets on both sides to maintain a reliable seal and prevent leakage.
Uneven Tightening Force or Failure to Tighten Flange Bolts:
Ensure uniform force while tightening flange bolts to maintain even pressure on the flanges, effectively resolving leakage issues at both ends.
Failure of Upper and Lower Sealing Ring Gaskets:
Replace the gaskets that have failed on the upper and lower parts of the valve, ensuring complete sealing at both ends.
3. External Leakage at the Packing AreaReplace the faulty sealing gaskets on both sides to maintain a reliable seal and prevent leakage.
Uneven Tightening Force or Failure to Tighten Flange Bolts:
Ensure uniform force while tightening flange bolts to maintain even pressure on the flanges, effectively resolving leakage issues at both ends.
Failure of Upper and Lower Sealing Ring Gaskets:
Replace the gaskets that have failed on the upper and lower parts of the valve, ensuring complete sealing at both ends.
Overdue Use of Packing Material, Resulting in Aging:
Timely replacement of aged or damaged packing material, with careful installation at an angle of 30-45 degrees to enhance the lifespan of the packing material.
Excessive Force Applied During Operation:
Operate the valve with uniform force, avoiding the use of additional sleeves or methods to extend the force arm, thus minimizing the possibility of packing leakage.
Failure to Tighten the Packing Sleeve Bolts:
Evenly tighten the bolts securing the packing to ensure a tight seal, preventing external leakage at the packing area.
Timely replacement of aged or damaged packing material, with careful installation at an angle of 30-45 degrees to enhance the lifespan of the packing material.
Excessive Force Applied During Operation:
Operate the valve with uniform force, avoiding the use of additional sleeves or methods to extend the force arm, thus minimizing the possibility of packing leakage.
Failure to Tighten the Packing Sleeve Bolts:
Evenly tighten the bolts securing the packing to ensure a tight seal, preventing external leakage at the packing area.
4. Damage to Handles and Handwheels
Incorrect Usage:
Prohibit the use of pipe wrenches, long levers, and impact tools to prevent damage to handles and handwheels.
Loosening of Fasteners:
Regularly inspect and tighten fasteners to ensure handles and handwheels remain secure.
Damage to the Connection Between Handles, Handwheels, and Valve Stem:
Promptly repair any damage to the connection between handles, handwheels, and the valve stem to ensure smooth and accurate operation.
5. Turbine and Turbine Rod Drive JammingProhibit the use of pipe wrenches, long levers, and impact tools to prevent damage to handles and handwheels.
Loosening of Fasteners:
Regularly inspect and tighten fasteners to ensure handles and handwheels remain secure.
Damage to the Connection Between Handles, Handwheels, and Valve Stem:
Promptly repair any damage to the connection between handles, handwheels, and the valve stem to ensure smooth and accurate operation.
Contamination Causing Poor Lubrication:
Regularly clean contaminants embedded in the turbine, ensuring a clean environment, and apply lubrication regularly.
Poor Operation:
If jamming is detected during operation with significant resistance, immediately cease operations and conduct a thorough inspection to prevent further complications.
Regularly clean contaminants embedded in the turbine, ensuring a clean environment, and apply lubrication regularly.
Poor Operation:
If jamming is detected during operation with significant resistance, immediately cease operations and conduct a thorough inspection to prevent further complications.
6. Electric Installation Failures
Poor Lubrication, Foreign Objects Blocking the Valve, Resulting in Excessive Torque and Damage: Regularly lubricate, maintain proper oil flow, and promptly remove foreign objects from the valve to prevent damage due to excessive torque.
Motor Malfunctions:
Limit the working time of the motor to no more than 15 minutes, ensure a stable power supply, and prevent the motor from being exposed to moisture to avoid electric installation failures.
Motor Malfunctions:
Limit the working time of the motor to no more than 15 minutes, ensure a stable power supply, and prevent the motor from being exposed to moisture to avoid electric installation failures.
By thoroughly understanding the potential causes of various butterfly valve failures and implementing these detailed solutions, we can effectively manage and maintain these crucial fluid control devices, ensuring prolonged and efficient operation.