Comparing Knife Gate Valves and Globe Valves in Industrial Systems
Knife gate valves and globe valves are integral components in industrial systems, serving as crucial shut-off valves. While both types regulate fluid flow, they diverge significantly in design, operation, and maintenance requirements. In this exploration, we'll delve into the unique attributes of knife gate valves and globe valves, encompassing their structural disparities, sealing mechanisms, flow characteristics, flow direction adaptability, and maintenance considerations.
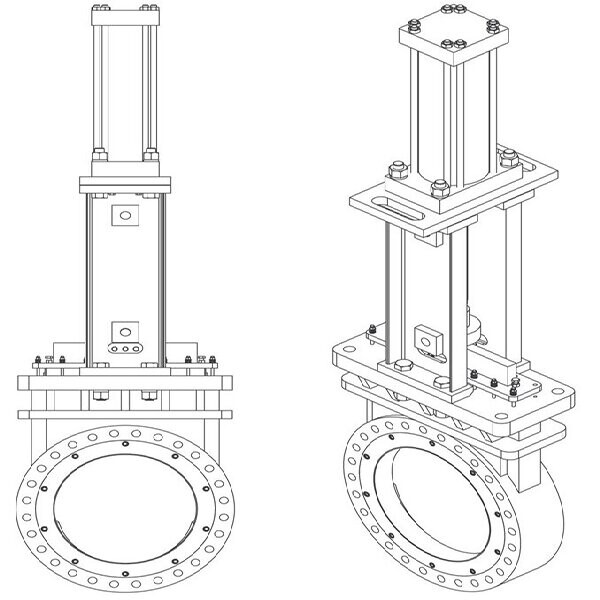
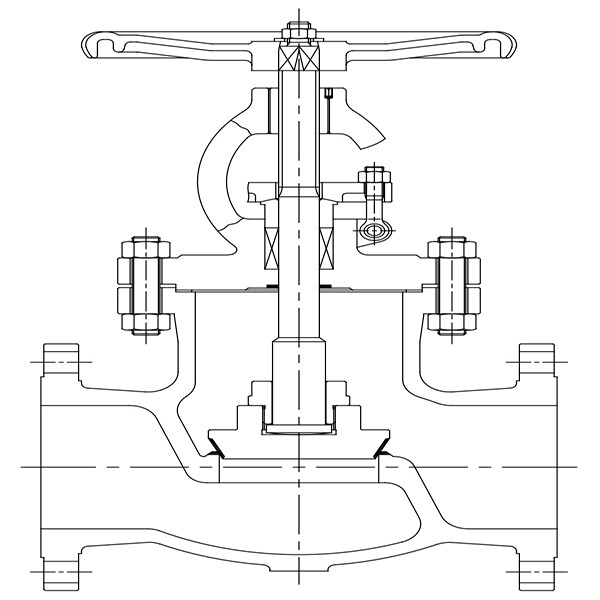
1. Structural Variations
Knife gate valves typically embody greater intricacy and larger dimensions compared to globe valves. Featuring a gate or wedge mechanism, knife gate valves present a robust yet intricate design. In contrast, globe valves boast a more compact and straightforward construction, making them well-suited for space-constrained installations.
2. Sealing Mechanisms
Operating with a gate in constant contact with the valve seat, knife gate valves may experience wear and tear on the sealing surfaces, especially under high-pressure conditions. Conversely, globe valves incorporate a disc that disengages from the valve seat when in the open position, mitigating mechanical wear. However, they remain vulnerable to damage from solid particles in the fluid.
3. Flow Resistance
Knife gate valves offer minimal flow resistance when fully open, ideal for applications where frequent operation is unnecessary. However, they lack flow regulation capabilities. Conversely, globe valves exhibit significant flow resistance throughout their stroke, making them suitable for flow regulation tasks albeit requiring a higher driving force.
4. Flow Direction Flexibility
Globe valves afford flexibility in adjusting flow direction, accommodating fluid entry from below or above the valve disc. This adaptability simplifies installation and operation across diverse settings. Conversely, knife gate valves maintain consistent effectiveness regardless of the fluid entry direction.
5. Maintenance Considerations
While knife gate valves generally lack provisions for on-site repairs, globe valves often facilitate seat and disc replacement without necessitating removal of the entire valve assembly. This feature streamlines maintenance tasks, ensuring operational efficiency with minimal disruption.
In summary, knife gate valves and globe valves exhibit distinct attributes in terms of structural design, sealing mechanisms, flow characteristics, flow direction adaptability, and maintenance requirements. Thus, meticulous consideration of these factors is imperative for selecting and deploying valves that guarantee optimal performance and reliability within industrial systems.