Understanding External Sealing Technologies in Industrial Valves
External sealing in valves refers to the sealing measures implemented at the junction of the valve cover and stem. This aspect plays a critical role in the overall sealing performance of industrial valves, directly impacting their safety and reliability within industrial operations. Within the realm of external sealing technology in industrial valves, there exist two primary structures: forced sealing and pressure self-sealing. This article aims to delve into the distinctive characteristics, diverse applications, and prudent selection principles governing these two sealing methodologies.
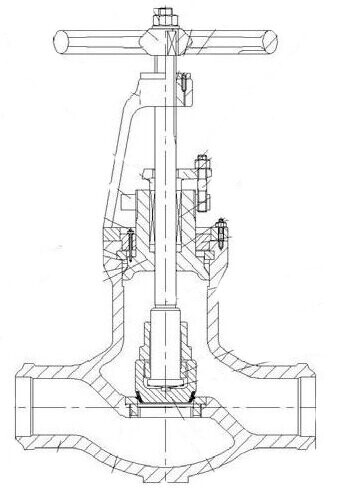
1. Forced Sealing Technology
Forced sealing operates by applying pressure through tightening the valve cover bolts. This pressure compresses the sealing gasket, effectively filling the minute crevices on the sealing surface to ensure valve integrity. As the medium pressure increases or the valve undergoes operational adjustments, the pressure on the sealing surface diminishes, allowing the sealing gasket to rebound. The efficacy of this rebound, dictated by the gasket's resilience, is pivotal in maintaining the valve's sealing performance. Forced sealing finds optimal application in medium to low-pressure scenarios and valves of small to medium dimensions. Typical embodiments encompass flat gasket seals, spiral wound gasket seals, and serrated gasket seals, among others.
2. Pressure Self-Sealing Technology
Pressure self-sealing emerges as a high-pressure sealing solution, frequently employed in valves operating under high-temperature and high-pressure conditions. A quintessential representation of this technology is the wedge-shaped gasket combination self-sealing structure. Here, the pre-tightening of bolts establishes initial sealing conditions between the valve cover and the wedge-shaped sealing gasket. As the medium pressure escalates, the sealing-to-pressure ratio gradually amplifies, culminating in the valve's self-sealing mechanism. This technology finds widespread utilization in high-pressure valves across industries such as refining and chemical processing.
3. Sealing Materials and Selection Criteria
The judicious selection of sealing materials is imperative to ensure optimal sealing performance. In pressure self-sealing technology, the selection criteria for wedge-shaped gaskets entail maintaining corrosion resistance and high-temperature tolerance, while ensuring a surface hardness lower than that of the valve body and cover sealing layers. This characteristic facilitates facile plastic deformation while upholding adequate strength. A common practice involves plating a layer of soft material or coating onto the surface of the wedge-shaped gasket to augment its contact area and angle differential with the valve body, thereby enhancing the sealing efficacy.
In conclusion, forced sealing and pressure self-sealing stand as the primary technologies governing external valve sealing, each offering distinct attributes and finding extensive utility across various industrial domains. When navigating the selection of sealing structures and materials, a judicious approach, informed by specific operational exigencies and performance requirements, is paramount to ensuring the seamless operation and enduring sealing integrity of valves.
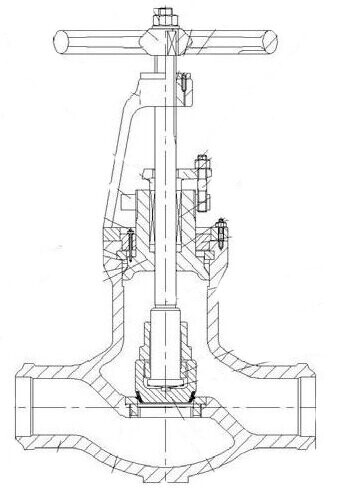
1. Forced Sealing Technology
Forced sealing operates by applying pressure through tightening the valve cover bolts. This pressure compresses the sealing gasket, effectively filling the minute crevices on the sealing surface to ensure valve integrity. As the medium pressure increases or the valve undergoes operational adjustments, the pressure on the sealing surface diminishes, allowing the sealing gasket to rebound. The efficacy of this rebound, dictated by the gasket's resilience, is pivotal in maintaining the valve's sealing performance. Forced sealing finds optimal application in medium to low-pressure scenarios and valves of small to medium dimensions. Typical embodiments encompass flat gasket seals, spiral wound gasket seals, and serrated gasket seals, among others.
2. Pressure Self-Sealing Technology
Pressure self-sealing emerges as a high-pressure sealing solution, frequently employed in valves operating under high-temperature and high-pressure conditions. A quintessential representation of this technology is the wedge-shaped gasket combination self-sealing structure. Here, the pre-tightening of bolts establishes initial sealing conditions between the valve cover and the wedge-shaped sealing gasket. As the medium pressure escalates, the sealing-to-pressure ratio gradually amplifies, culminating in the valve's self-sealing mechanism. This technology finds widespread utilization in high-pressure valves across industries such as refining and chemical processing.
3. Sealing Materials and Selection Criteria
The judicious selection of sealing materials is imperative to ensure optimal sealing performance. In pressure self-sealing technology, the selection criteria for wedge-shaped gaskets entail maintaining corrosion resistance and high-temperature tolerance, while ensuring a surface hardness lower than that of the valve body and cover sealing layers. This characteristic facilitates facile plastic deformation while upholding adequate strength. A common practice involves plating a layer of soft material or coating onto the surface of the wedge-shaped gasket to augment its contact area and angle differential with the valve body, thereby enhancing the sealing efficacy.
In conclusion, forced sealing and pressure self-sealing stand as the primary technologies governing external valve sealing, each offering distinct attributes and finding extensive utility across various industrial domains. When navigating the selection of sealing structures and materials, a judicious approach, informed by specific operational exigencies and performance requirements, is paramount to ensuring the seamless operation and enduring sealing integrity of valves.