Pros & Cons of Common Materials Used in Industrial Valves
On this page
Industrial valves are core components in fluid control systems, and their material directly affects performance, durability, and suitability for various applications. Different valve materials have their own strengths and weaknesses depending on the operating conditions, such as temperature, pressure, and the nature of the media. Below is a detailed analysis of common valve materials, highlighting their characteristics and suitability for different working conditions.
Cast iron valves are made from cast iron, which is affordable and easy to manufacture, making them a popular choice for low-cost projects. Cast iron is easy to cast and works well with common media such as water, steam, and oil under normal temperature and low-pressure conditions.
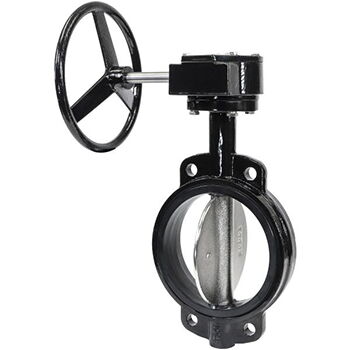
Cost-Effective: Cast iron is inexpensive to produce, making these valves affordable for budget-limited projects.
Ease of Processing: Cast iron is easy to cast into various shapes, meeting different design requirements.
Wide Application: Suitable for handling water, steam, and oil at normal temperatures and low pressures, providing good fluid control.
Low Strength and Toughness: Cast iron lacks the strength and toughness needed for high-pressure, high-temperature, or impact-heavy conditions, leading to possible cracking or deformation.
Poor Corrosion Resistance: Cast iron valves are not resistant to strong acids or alkalis, leading to potential damage and reduced lifespan in corrosive environments.
Cast steel valves are made from steel, offering high strength and hardness. They are ideal for high-pressure, high-temperature environments and are commonly used in industries such as petrochemical and power generation.
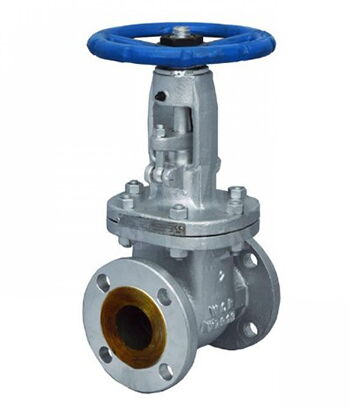
High Strength and Impact Resistance: Cast steel can withstand higher pressures and impacts, making it suitable for harsh conditions like high temperatures and pressures.
Wide Application: Can handle various media such as water, steam, oil, and chemicals.
Good Toughness: Unlike cast iron, cast steel has better toughness, making it less prone to brittle fractures under force.
Higher Cost: The manufacturing process for cast steel is more complex, and the raw material is more expensive, making these valves costly.
Heavy Weight: Cast steel is denser, which results in heavier valves, increasing transportation and installation costs.
Stainless steel valves are made from alloys containing chromium and nickel, offering excellent corrosion resistance. They are ideal for industries that require high corrosion resistance and hygiene standards, such as chemicals, food, and pharmaceuticals.
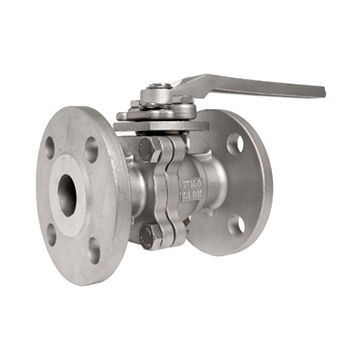
Superior Corrosion Resistance: Stainless steel resists most acids, alkalis, and salts, making it perfect for use in chemical and food industries.
High-Temperature Stability: It retains good mechanical and corrosion-resistant properties even at high temperatures, suitable for steam and heat treatment systems.
Ease of Cleaning and Maintenance: The smooth surface of stainless steel makes it easy to clean, ensuring consistent performance and hygiene.
Higher Cost: Stainless steel, particularly special grades, is expensive, raising the initial cost of the valves.
Difficult to Process: Stainless steel has a high hardness, making it difficult to machine, which can increase production time and costs.
Copper valves are known for their excellent thermal and electrical conductivity. They are widely used in temperature-sensitive applications like heating and air conditioning systems and can also handle non-corrosive media such as freshwater and seawater.
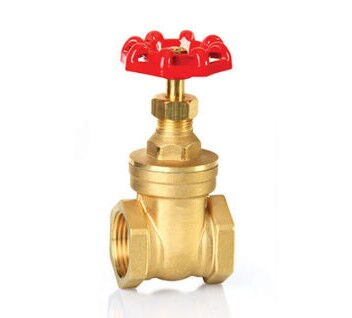
Excellent Thermal and Electrical Conductivity: Copper is ideal for use in systems requiring temperature control or electrical connections.
Good Corrosion Resistance: Copper is stable in non-corrosive media like freshwater and seawater, providing reliable long-term performance.
Good Workability: Copper is easy to shape and mold, making it versatile for different installation and usage needs.
Low Strength and Hardness: Copper has lower strength, so it is not suitable for high-pressure or high-load conditions, where it may deform or break.
Price Fluctuations: Copper prices are subject to market demand and can fluctuate, leading to cost unpredictability.
Plastic valves are valued for their corrosion resistance and lightweight nature. They are commonly used in systems transporting corrosive media, such as wastewater treatment and certain chemical processes.
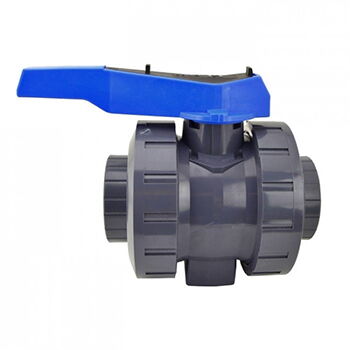
Corrosion Resistance: Plastic valves are resistant to a wide range of chemicals, making them suitable for handling corrosive media.
Lightweight: Their low density makes plastic valves easy to install and transport, reducing labor and transportation costs.
Low Cost: Plastic materials are inexpensive, making these valves cost-effective for various applications.
Electrical Insulation: Plastic is an excellent electrical insulator, useful in environments requiring electrical isolation.
Low Mechanical Strength: Plastic has limited strength and heat resistance, making it unsuitable for high-pressure or high-temperature applications.
Aging: Plastic materials can degrade over time due to UV exposure or oxygen, shortening the valve's lifespan and reducing its performance.
Ceramic valves are made from high-hardness ceramic materials, offering excellent wear resistance and corrosion resistance. They are particularly suited for handling media with solid particles, such as slurry and coal powder.
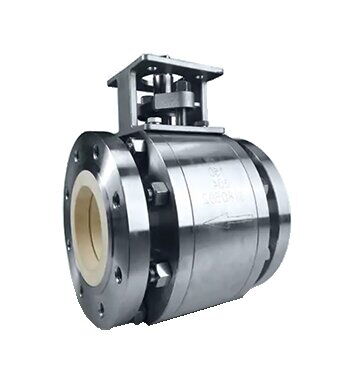
High Wear Resistance: Ceramic materials have excellent hardness, significantly reducing wear in high-abrasion environments, such as slurry and coal powder transport.
Corrosion Resistance: Ceramic can withstand most acids, alkalis, and salts, making it suitable for harsh chemical environments.
High-Temperature Resistance: Ceramics can handle high-temperature media, making them useful in power and metallurgy industries.
Safe and Hygienic: Ceramic materials do not release harmful substances, making them ideal for applications like drinking water treatment and food processing.
Brittleness: Ceramic is brittle and can break under impact or uneven load, limiting its use in environments with frequent operation or vibration.
High Cost: High-quality ceramics are expensive to produce, making ceramic valves costly compared to metal valves.
When choosing valve materials, it's important to consider the operating conditions, budget, and material characteristics. Cast iron valves are suitable for low-pressure, normal-temperature conditions, while cast steel valves excel in high-pressure, high-temperature environments. Stainless steel valves are ideal for corrosion-resistant applications, and copper valves perform well in temperature-controlled systems. Plastic valves are well-suited for low-pressure, corrosive media, while ceramic valves stand out in high-abrasion and high-corrosion environments. Ultimately, the selection should be based on specific operational requirements, economic considerations, and performance needs.