Metal Seated Ball Valves for Superior High-Temperature Sealing
Metal seated ball valves are crucial ball valves for achieving effective high-temperature sealing, particularly in industries such as chemical engineering, petrochemicals, and thermal power generation. Renowned for their versatility, these ball valves excel in diverse process conditions. This article delves into the crucial role of metal seated ball valves, emphasizing key design considerations and addressing wear challenges in demanding environments.
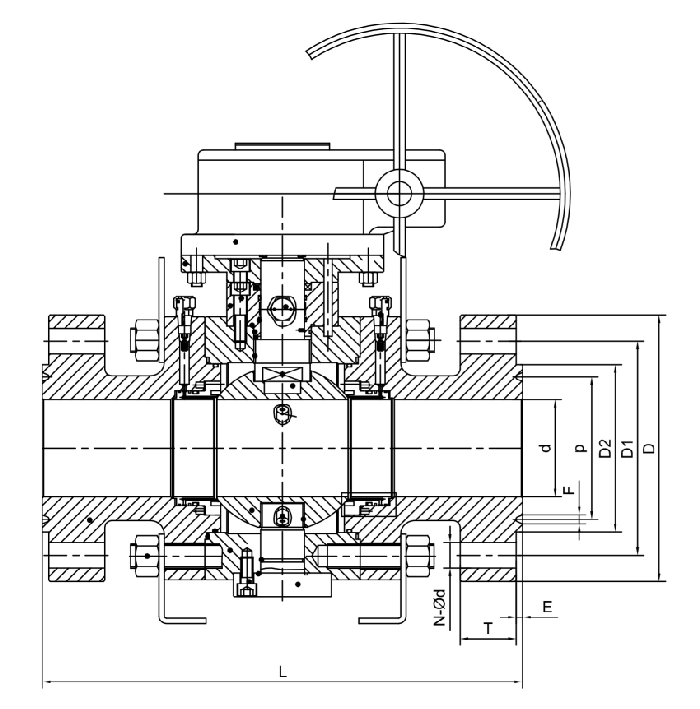
1. Pressure and Structural Design
In these industrial sectors, pipeline valves must withstand not only extremely high temperatures but also specific pressure ratings, which are crucial for their operational viability. Specialized structural designs play a pivotal role in enhancing the pressure ratings that valves can withstand. For instance, the Trunnion structure or designs with insulating layers can increase the valve's pressure resistance, thereby enhancing its stability and safety.
2. Criticality of Sealing Systems
The key to metal-seated, metal-to-metal sealed pipeline valves lies in the interaction between the ball valve core and the sealing system. One common sealing system employs metal seated seals, such as cobalt-chromium-tungsten alloy seals, known for their high corrosion resistance, extended lifespan, and superior wear resistance. For pipeline valves relying on metal sealing surfaces, the paramount requirement is zero leakage, or at least performance equal to that of conventional ball valves. Hence, users prioritize wear resistance when selecting metal-sealed ball valves.
3. Types of Wear and Countermeasures
Wear is a significant challenge faced by metal-seated, metal-to-metal sealed ball valves during operation and can be categorized into adhesive wear, abrasive wear, and surface corrosion wear.
4. Elevated Design Requirements
In addition to the demand for erosion resistance, features like automatic pressure relief and compensation for ball valve sealing have become increasingly crucial, serving as core considerations for long-term, reliable operation. Automatic pressure relief refers to the discharge of excessive pressure within the sealed space behind the ball valve core through the sealing system, where the design of elastic structures plays a significant role.
In summary, metal-seated ball valves play an indispensable role in providing high-temperature sealing performance in process industries. Through optimized structural design and sealing system improvements, the challenges of wear and other issues can be effectively addressed, ensuring the stable operation of valves and providing reliable support for industrial production.
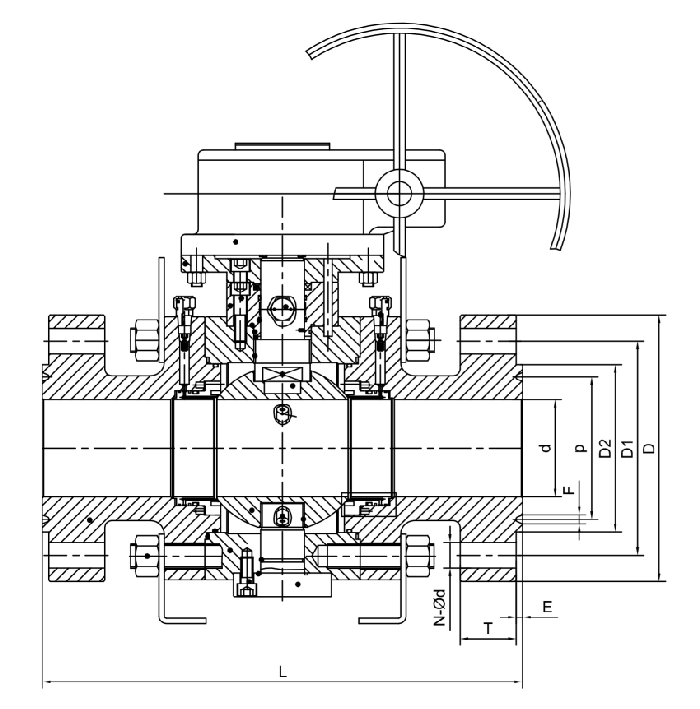
1. Pressure and Structural Design
In these industrial sectors, pipeline valves must withstand not only extremely high temperatures but also specific pressure ratings, which are crucial for their operational viability. Specialized structural designs play a pivotal role in enhancing the pressure ratings that valves can withstand. For instance, the Trunnion structure or designs with insulating layers can increase the valve's pressure resistance, thereby enhancing its stability and safety.
2. Criticality of Sealing Systems
The key to metal-seated, metal-to-metal sealed pipeline valves lies in the interaction between the ball valve core and the sealing system. One common sealing system employs metal seated seals, such as cobalt-chromium-tungsten alloy seals, known for their high corrosion resistance, extended lifespan, and superior wear resistance. For pipeline valves relying on metal sealing surfaces, the paramount requirement is zero leakage, or at least performance equal to that of conventional ball valves. Hence, users prioritize wear resistance when selecting metal-sealed ball valves.
3. Types of Wear and Countermeasures
Wear is a significant challenge faced by metal-seated, metal-to-metal sealed ball valves during operation and can be categorized into adhesive wear, abrasive wear, and surface corrosion wear.
Adhesive and Abrasive Wear: Adhesive wear results from direct chemical and mechanical contact reactions between the ball valve core and the metal sealing seat. Through precise machining processes and matching, a degree of wear reduction can be achieved, but some level of wear is inevitable over time.
Surface Corrosion: Surface corrosion occurs due to electrochemical reactions between the chemical components of the conveyed medium and the metal surface of the valve. For valves relying on metal surface sealing, localized surface corrosion poses the greatest risk, potentially leading to valve damage. To address this issue, careful attention to the chemical composition of the medium and appropriate protective measures are essential.
Surface Corrosion: Surface corrosion occurs due to electrochemical reactions between the chemical components of the conveyed medium and the metal surface of the valve. For valves relying on metal surface sealing, localized surface corrosion poses the greatest risk, potentially leading to valve damage. To address this issue, careful attention to the chemical composition of the medium and appropriate protective measures are essential.
4. Elevated Design Requirements
In addition to the demand for erosion resistance, features like automatic pressure relief and compensation for ball valve sealing have become increasingly crucial, serving as core considerations for long-term, reliable operation. Automatic pressure relief refers to the discharge of excessive pressure within the sealed space behind the ball valve core through the sealing system, where the design of elastic structures plays a significant role.
In summary, metal-seated ball valves play an indispensable role in providing high-temperature sealing performance in process industries. Through optimized structural design and sealing system improvements, the challenges of wear and other issues can be effectively addressed, ensuring the stable operation of valves and providing reliable support for industrial production.