Bellows Sealed Valves: Key Features & Industrial Applications
On this page
Bellows sealed valves are high-performance valves widely used across various industrial sectors, particularly in applications where sealing integrity is crucial. The design of these valves takes into account both material selection and structural optimization to ensure reliability and stability in environments characterized by high pressure, high temperature, and corrosive media. This article will explore the working principles, design features, and application fields of bellows sealed valves in detail.
The design and functionality of bellows sealed valves depend on the precise coordination of their main components and the choice of high-quality materials.
The valve body and bonnet are typically made from cast steel or stainless steel. Cast steel is favored for its high strength and toughness, making it suitable for heavy-duty industrial environments, while stainless steel is chosen for its excellent corrosion resistance, especially in the chemical and food industries. The body design must not only withstand operating pressure but also facilitate a well-optimized fluid passage to reduce flow resistance.
The stem serves as the actuator for opening and closing the valve, utilizing rotary or linear motion to control the valve's state. It is generally made from stainless steel to ensure corrosion resistance and mechanical strength under harsh conditions. The design of the stem accounts for the precision of its fit with the bellows and the seat, enabling effective sealing.
The bellows are the key sealing elements of the valve, typically made from soft metallic materials like stainless steel or alloys. Their design provides excellent elasticity and corrosion resistance, maintaining effective sealing during the opening and closing processes to prevent media leakage.
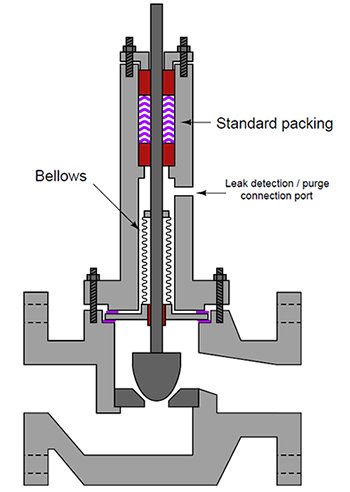
The working principle of bellows sealed valves relies on the elastic deformation of the bellows. When the valve is closed, the stem applies pressure to the bellows, causing it to deform elastically and tightly conform to the seat, forming an effective sealing barrier. This mechanism effectively prevents media leakage, ensuring the safety and stability of the system. Conversely, when the valve is opened, the stem lifts the bellows, allowing it to return to its original shape, thereby facilitating the smooth flow of media.
The design and structural characteristics of bellows sealed valves ensure exceptional performance in sealing capability, service life, and ease of operation, evident in several aspects.
Compactness: The structural design of bellows sealed valves is simple and compact, with the body and bonnet connected by double-headed studs. This design reduces manufacturing and maintenance complexity while enhancing the overall stability of the valve.
Fluid Passage Optimization: The fluid passages are carefully designed to minimize flow resistance, ensuring that the valve does not significantly impact flow during opening and closing.
Bellows Sealing: The bellows, as the main sealing component, are designed to form a reliable seal through elastic deformation when the valve is closed. This design significantly reduces the likelihood of leakage, ensuring system safety.
Dual Sealing System: In addition to the bellows, the valve features a dual sealing design using packing and bellows, achieving a zero-leakage effect and further enhancing sealing performance.
Surface Treatment: The stem nut undergoes nitriding treatment to increase surface hardness and wear resistance. This treatment effectively prevents galling during opening and closing, ensuring smooth operation.
Bellows Material: The bellows are typically made from highly corrosion-resistant metals, effectively resisting performance degradation in harsh environments. The design often incorporates 2 to 4 layers of overlapping bellows to prevent leakage from damage to a single layer.
Low Operating Torque: Bellows sealed valves are designed to require a small operating torque for opening and closing, making operation more flexible and enabling easy remote control and automation.
High Opening and Low Flow Resistance: The extended design of the bellows and high opening height reduce the primary flow resistance, resulting in a low flow resistance coefficient and improved flow efficiency.
Due to their superior sealing performance and durability, bellows sealed valves are widely used in multiple industries, including but not limited to the following:
Chemical Industry: In chemical processes, bellows sealed valves effectively control the flow of media, preventing leaks of corrosive substances and ensuring the safety of production. Their excellent sealing performance makes them core components in chemical equipment.
High Vacuum Systems: In high vacuum environments, the design of bellows sealed valves ensures a leak-free system, making them ideal for maintaining high vacuum conditions. Their superior elasticity and pressure resistance allow them to perform exceptionally in high vacuum applications.
Food and Pharmaceutical Industries: Due to their excellent hygiene and corrosion resistance, bellows sealed valves are widely used in the food and pharmaceutical sectors, effectively preventing product contamination and ensuring the safety of production processes.
Bellows sealed valves, with their outstanding sealing capabilities, simplified structural design, and diverse material options, have become essential equipment in modern industries. Whether in nuclear applications, high vacuum environments, or the chemical, food, and pharmaceutical industries, the use of bellows sealed valves ensures the safety and stability of systems. With continuous technological advancements, bellows sealed valves are expected to exhibit greater potential and value in future industrial applications. Ongoing improvements in design and manufacturing will further enhance their performance under various complex conditions, driving the development and progress of industrial technology.