Principles and Common Faults of Pneumatic Valves
On this page
In modern industrial automation systems, pneumatic valves are essential due to their efficient control and reliable performance. Using compressed air and a cylinder actuator, these valves precisely manage fluid flow and control valve operations. Despite their reliability, pneumatic valves can experience faults during operation. Understanding these issues and their solutions is crucial for maintaining efficient performance and extending service life. This article explores the working principle of pneumatic valves, common faults, and effective strategies for resolution.
Pneumatic valves are control devices that use compressed air as a driving force and are widely used in industrial automation systems. The basic working principle is as follows.
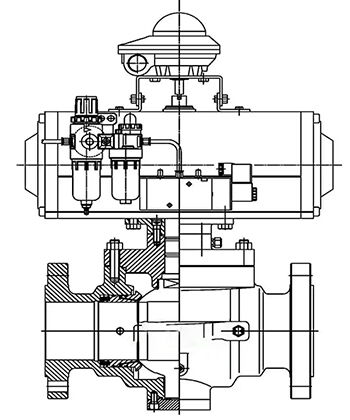
The regulator in the system receives a pressure signal of 0.02 to 0.10 MPa and converts it into mechanical action. This signal is the air pressure controlled by the air source, which is transmitted to the actuator part of the pneumatic valve.
The received air pressure signal acts on the diaphragm of the pneumatic valve, causing the diaphragm to generate corresponding thrust. This thrust directly acts on the thrust disc, pushing it to move downward.
The downward movement of the thrust disc compresses the spring. During this process, the spring stores mechanical energy, providing the necessary force for the operation of the valve.
The compressive force of the spring pushes the valve stem and push rod downward, thereby driving the valve core to adjust vertically. The movement of the valve core changes the opening of the valve, thereby regulating the flow of the fluid or completely closing the valve.
Pneumatic valves can achieve rapid response and high-precision control, suitable for various industrial applications such as flow regulation and on-off operations, including fields like chemical engineering, petroleum, pharmaceuticals, and food processing. The advantages of these valves lie in their efficient regulation capabilities and stable performance, making them an indispensable part of the automated control system.
Pneumatic valves may encounter some common faults during operation, including leakage, unstable movement, and sluggish action. Understanding the causes of these faults and their solutions helps to improve the reliability and performance of the equipment.
Leakage in pneumatic valves is usually caused by wear of the valve core or foreign objects inside. As the valve core wears over time, it may not seal completely when the valve is closed, increasing the leakage. Additionally, the presence of foreign objects inside the valve body or the sintering of the lining can also lead to a decrease in sealing performance, especially under high pressure differential conditions.
Solutions:
Regularly inspect the wear condition of the valve core and replace or repair as needed.
Maintain cleanliness inside the valve to prevent foreign objects from entering. Regularly clean the inside of the valve body and check the state of the lining to ensure its normal operation.
Unstable movement of the valve is mainly related to the stability of the signal pressure and the air source pressure. If the signal pressure fluctuates, it can cause unstable output from the regulator, affecting the precision of the valve's movement. At the same time, unstable air source pressure may lead to insufficient compressor capacity and malfunction of the pressure reducing valve. The position of the amplifier jet group in the positioner not being parallel, or the output pipeline not being airtight, can also lead to unstable valve movement.
Solutions:
Ensure the stability of the signal pressure, which can be achieved by using a pressure stabilizer to reduce fluctuations.
Check the stability of the air source system to ensure the normal operation of the compressor and pressure reducing valve. Regularly maintain the air source system to prevent insufficient pressure.
Calibrate and maintain the positioner to ensure that all parts are correctly positioned and tightened, and check the airtightness of the output pipeline.
Sluggish action is usually related to the bending of the valve stem and packing issues. Bending of the valve stem increases friction, making the valve's movement slow. In addition, poor lubrication of the packing or dust accumulation inside the valve body can also increase the operating resistance of the valve stem, leading to sluggish movement.
Solutions:
Check the straightness of the valve stem, and if bending is found, correct or replace it.
Use appropriate packing materials and maintain good lubrication performance. Regularly clean the dust inside the valve body to ensure smooth operation of the valve stem.
The stability of the air source and signal is the foundation for the normal operation of the pneumatic valve. If the air source is insufficient or the signal is missing, it may directly affect the performance of the valve. For example, if the positioner has no air source, it may cause the pressure reducing valve to malfunction, and in severe cases, it may lead to blockage of the filter and pipeline. If the air source is present but the signal is missing, it may damage the regulating diaphragm, causing the positioner to leak air.
Solutions:
Ensure sufficient air supply, especially in low-temperature environments, to prevent the air source and signal system from failing due to low temperatures.
Check and maintain the air source and signal system to ensure their normal operation. Regularly inspect the air source system to ensure there are no blockages or leaks.
By thoroughly understanding the working principles and common faults of pneumatic valves, one can effectively identify and solve problems encountered in practical applications, ensuring the efficient and stable operation of the pneumatic valve system. This not only helps to extend the service life of the equipment but also improves the reliability and safety of the entire system.