How to Prevent and Handle Gate Valve Leaks
Ensuring the prevention of leaks is crucial in the operation and maintenance of any industrial equipment. Within gate valve systems, inspecting and addressing leakage issues is particularly indispensable. This article will focus on how to inspect gate valves and connecting bolts, handle leaks in valve covers, valve body leaks, and leaks between valve seats and discs, to help ensure the smooth and safe operation of systems.
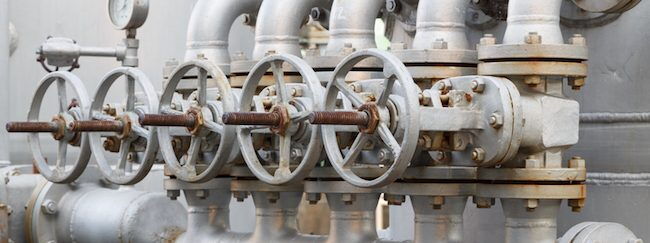
1. Inspecting Gate Valves and Connecting Bolts
Firstly, check if gate valves and connecting bolts are properly tightened. Improperly tightened bolts may result in incomplete compression between gasket rings and flange sealing surfaces, leading to leaks. Sequentially inspect bolts and nuts, ensuring all bolts are securely fastened to ensure proper compression of gaskets. Next, examine the dimensions and accuracy of gaskets and flange sealing surfaces. Any inappropriate or excessively rough conditions should be promptly repaired or replaced.
2. Handling Leaks in Valve Covers
Leaks in valve covers may stem from inadequately secured body bolts, mainly manifesting at the packing seal. Initially, check if seals are correctly selected and matched with the seal groove; if mismatched, seals need replacement or seal groove repair. Then, carefully inspect seals for burrs, fractures, or distortions; if found, prompt replacement is necessary. Further, check for roughness or other defects on the sealing surface of each seal groove; if detected, eliminate or replace damaged components promptly. Another potential leak point might occur at the packing gland of the valve stem, requiring an inspection of the packing installation; if misaligned, reinstall according to the correct procedure.
3. Handling Valve Body Leaks
Valve body leaks typically arise from defects in the casting process, such as sand holes and blowholes, which are challenging to detect during machining but become evident under pressure. In such cases, repairs, refurbishment, or replacements of the valve body are necessary.
4. Handling Leaks between Valve Seats and Discs
Leaks between valve seats and discs commonly fall into two categories: surface sealing leaks and root leaks of sealing rings. Initially, meticulously inspect the accuracy of the sealing surfaces of valve seats and discs, ensuring they are at least flat. If surfaces are rough, clean and regrind them. Then, examine for defects such as pitting, indentations, blisters, or cracks on the sealing surfaces; if found, damaged components should be promptly replaced.
In conclusion, gate valve leaks may result not only from defects in processing and casting but also from foreign substances such as welding residues, iron scraps, and impurities during installation. Hence, thorough cleaning before installation is imperative. Failure to clean or incomplete cleaning may result in insufficient closure of the valve disc, leading to leaks, requiring disassembly of the valve body for thorough cleaning. Throughout any troubleshooting process, maintaining a systematic approach and meticulous inspection are crucial.