Effective Installation of Sealing Gaskets for Valves
On this page
Sealing gaskets are critical components in valve and piping systems, widely used across various industrial applications to ensure that media do not leak under different pressure and temperature conditions. As an essential accessory for valves, the correct installation of gaskets is directly related to the sealing performance and operational safety of the entire equipment. This article provides a detailed overview of gasket installation procedures, key considerations, and application guidelines for different types of gaskets, aiming to improve installation quality and sealing performance.
Prior to installing sealing gaskets, it is essential to thoroughly inspect the related equipment components, including flange connections, threaded connections, static sealing surfaces, and the gaskets themselves, to ensure that all parts are intact, clean, and smooth. If any damage, scratches, or irregularities are found, they should be repaired or replaced promptly. It is also necessary to lubricate the sealing surfaces, gaskets, and threaded areas before installation. Common lubricants include graphite powder or a mixture of graphite powder and engine oil (or water), which can reduce friction, prevent scratching and deformation during installation, and enhance sealing performance.
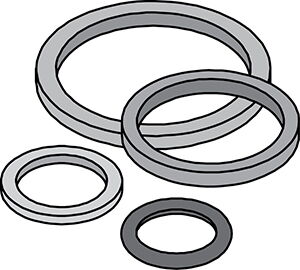
The correct installation of gaskets is crucial as it directly affects the performance and reliability of the sealing system, as well as the operational safety and service life of the equipment. To ensure effective sealing, the following key steps should be followed.
During installation, the gasket must be precisely placed on the sealing surface, aligned with the center of the sealing surface, without any misalignment or offset. Any deviation or misalignment can lead to poor sealing or localized stress concentration, reducing sealing effectiveness and potentially causing leaks.
Only one gasket should be installed between any two sealing surfaces. Stacking multiple gaskets to compensate for insufficient clearance is strictly prohibited, as it can lead to sealing failure and may cause damage to the sealing surface or gaskets due to uneven stress distribution.
Oval Gaskets: When installing oval gaskets, ensure that the inner and outer rings are in close contact with the sealing surface, and that neither end face contacts the groove bottom. Otherwise, this can compromise the gasket's sealing performance and service life.
O-Rings: O-rings should be installed according to design specifications, ensuring proper compression. The compression deformation rate should be minimized while ensuring sealing, which helps extend the O-ring's service life and prevent premature aging or failure.
Before installing gaskets, the valve should be in the open position to prevent damage to components such as the valve disc or valve seat during installation. Avoid using pushing or pulling methods to move the gasket, as this can cause misalignment or scratches.
For bolt connections, ensure that the gasket is positioned horizontally, and the bolts should be tightened evenly and symmetrically during installation, gradually increasing the tightening force to prevent uneven stress on the gasket.
For threaded connections, if there is a dedicated wrench position on the gasket cover, use the appropriate tool to avoid damage to the gasket or threads caused by pipe wrenches or similar tools.
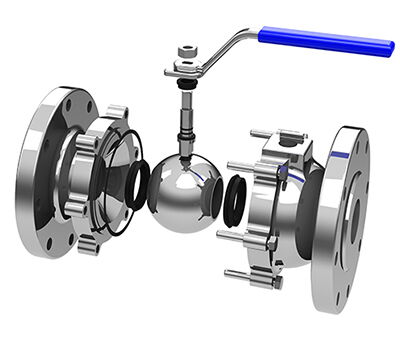
The compression force of the gasket is a key factor influencing sealing performance. Before compressing the gasket, it is essential to understand the system's pressure, temperature, medium characteristics, and gasket material properties to determine the appropriate preload force. Excessive or insufficient preload force can negatively impact the sealing effect. The correct preload force should ensure that there is no leakage during pressure testing while minimizing excessive compression of the gasket to avoid deformation and damage.
Thermal Tightening and Cold Relaxation: In high-temperature environments, bolts may experience creep relaxation due to thermal expansion, requiring timely "thermal tightening" operations. In low-temperature conditions, bolts may contract, necessitating appropriate loosening to prevent equipment damage due to excessive stress.
Different types of sealing gaskets are suitable for specific working environments and applications. Depending on the material and design characteristics of the gasket, they exhibit varying levels of performance and suitability for sealing liquids, gases, and high-temperature, high-pressure media.
For gaskets used to seal liquids, the sealing surface should be cleaned and treated before installation to ensure a smooth contact surface. The adhesive should be applied evenly, with a thickness typically controlled between 0.1 and 0.2 mm to eliminate air and ensure effective sealing.
For thread sealing, the starting point of the PTFE tape should be stretched thinly and adhered to the thread surface, then the excess should be removed to form a wedge shape on the thread, ensuring tight sealing.
In practice, several issues can arise during the use of sealing gaskets, affecting their sealing performance and the normal operation of the equipment. Below are some common problems and corresponding solutions:
Improper installation or poor gasket quality may lead to inadequate sealing or gasket damage. Check whether the sealing surface is smooth and flat, and whether the gasket is intact. Ensure that the gasket is not scratched or misaligned during installation.
Insufficient preload force can lead to leakage, while excessive force may damage the gasket. Adjust the bolt tightening force reasonably according to the medium characteristics and system requirements, and use a torque wrench to precisely control the tightening force when necessary.
Over time, especially in high-temperature and high-pressure environments, bolts may loosen or threads may become damaged, affecting sealing performance. Regularly check the bolt tightness and retighten or replace as needed.
The correct installation and maintenance of sealing gaskets are crucial for the safe and stable operation of valve and piping systems. During installation, it is essential to follow standard procedures, select and adjust the preload force reasonably, and regularly check the sealing condition to ensure long-term reliability and effectiveness of the sealing system. Understanding the installation methods and key considerations for different types of gaskets can effectively prevent common issues and improve the operational efficiency and safety of the system.