Design and Performance Requirements of Three-Way Ball Valve Seats
On this page
Three-way ball valves play a crucial role in various industrial applications, and the valve seat, as a core component, significantly affects the overall performance and reliability of the ball valve. The design and material selection of the ball valve seat directly impact the valve's sealing performance, durability, and performance under harsh conditions. This article will comprehensively discuss the design requirements, performance characteristics, and future development trends of three-way ball valve seats.
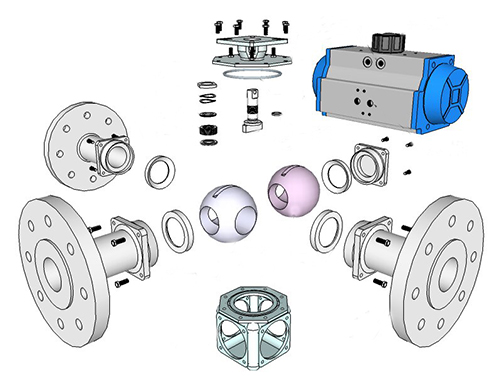
Hard seats are primarily used to achieve efficient sealing functions and have the following design requirements.
Hard seats need to have sufficient strength and rigidity to maintain stability under high pressure conditions. High-strength materials such as alloy steel and hard alloys are commonly used to manufacture hard seats to prevent deformation or rupture in high-pressure environments.
Hard seats should be able to withstand extreme temperature and pressure conditions. Seats designed with metal hard sealing can operate stably at temperatures up to 500°C, which is crucial for high-temperature pipeline systems in the oil, chemical, and power industries.
When dealing with media containing solid particles (such as mud, black water, coal powder, etc.), the valve seat needs to have excellent wear and corrosion resistance. The use of wear-resistant materials such as hard alloys can significantly extend the service life of the valve seat and reduce seal failure due to wear or corrosion.
The metal-to-metal hard sealing design of hard seats is demanding, usually achieved by hard-facing the seat surface with hard alloys to increase its hardness to 60HRC. This design ensures zero-leakage sealing performance and has fire safety features, maintaining the valve's sealing performance under extreme conditions such as fires.
Soft seals play a key role in soft-sealed three-way ball valves, and their design should consider the following aspects.
Soft seal materials include rubber, nylon, and polytetrafluoroethylene (PTFE), among others. Choosing the right material can provide excellent chemical stability, aging resistance, and low friction coefficient, which is crucial for maintaining long-term stable sealing performance.
Under specific contact pressures, soft seals undergo elastic-plastic deformation. This deformation can compensate for the shortcomings of the ball's manufacturing accuracy and surface roughness, ensuring stable sealing performance. However, this also means that the service life of the soft seal is limited by its material properties and the wear of the medium.
The operating temperature of soft seals is limited by their material properties. For example, the temperature resistance of rubber and nylon is relatively low, while PTFE has a broader temperature range. In high-temperature environments, choosing the appropriate sealing material is key to ensuring the normal operation of the valve.
In the fire-safe design of three-way ball valves, the fire-safe structure of the valve seat is particularly important to reduce medium leakage and prevent the spread of fire in the event of a fire accident.
The fire-resistant design of the valve seat can effectively reduce medium leakage in the event of a fire. By setting fire-safe rings between the seat and the ball, as well as between the seat and the valve body, it is possible to prevent medium leakage caused by fires.
The design of fire-safe rings can prevent medium leakage from the gap between the O-ring and the intermediate cavity in the event of a fire. By adding fire-resistant rings, the valve seat can maintain effective sealing during fire accidents and prevent the accident from escalating.
As energy competition intensifies and the long-distance pipeline industry develops, the design requirements for valve seats are also continuously improving.
Due to the increase in the production of viscous oil, three-way ball valve seats need to adapt to the room-temperature transportation process of high-viscosity and easily solidifying crude oil. This requires the valve seat to have higher wear resistance, corrosion resistance, and erosion resistance to cope with the challenges of high viscosity and solid particle media.
As natural gas pipelines develop towards large diameters and high pressures, the valve seat's high-pressure resistance and sealing stability become particularly important. The valve seat needs to have high strength and high-pressure resistance to ensure stable operation under high-pressure environments.
To meet the market's demand for high-performance valve seats, the design of valve seats must continue to innovate to adapt to more severe working environments and higher performance requirements. For example, special designs for extreme environments and the application of new materials will become the focus of future development.
In conclusion, the design of three-way ball valve seats is essential for valve performance and reliability. Hard seats offer stability in extreme conditions with their strength, temperature resistance, and sealing capabilities. Soft seals complement this with effective sealing through material selection and deformation adaptability. As the energy sector and pipeline technologies advance, the demands on valve seats intensify, necessitating designs that can withstand higher temperatures, pressures, and corrosive environments. Continuous innovation in materials and technology will ensure valve seats meet evolving market needs, thereby guaranteeing the efficiency and safety of industrial processes.